製造業における在庫管理のやり方と基礎知識
在庫管理の基礎知識、やり方や考え方・技法を習得して運用することは、製造業にとっては特に重要な項目の一つで、一般には生産管理や物流・ロジスティックス部門、購買管理部門、貿易部門、経理部門(棚卸)と縁の深い分野です。ここでは在庫管理の目的や定義からはじまり、会社経営上のインパクト、その手法や見るべきポイントを幅広くご紹介していきます。また在庫の問題はメーカー、流通、卸、小売と「モノ」を扱うほぼすべての業種に共通するテーマですが、ここでは最後にメーカーや製造分野で固有に起きる在庫上の問題についても触れていきます。在庫管理をはじめて間もない方やこれからはじめようとされる方で特にモノづくりにかかわる業種としてどのように取り組んでいくべきかの指針になれば幸いです。
在庫管理の定義
在庫管理はJISでは次のように定義されています。「必要な資材を、必要なときに、必要な量を、必要な場所へ供給できるように、各種品目の在庫を好ましい水準に維持するための諸活動」。在庫管理の方式としては、定量発注方式と定期発注方式に大別されることになります。
さらにこれを詳しくみていくと、在庫管理の具体的な仕事内容は「倉庫内における在庫品の物理的な管理業務=現物管理」と「どれくらいの在庫数でどのように運用・発注するかという在庫数量の管理業務」の大きく2つに定義づけられます。どう定義するかで仕事内容や目的も異なりますので、まずどちらにウェイトを置くのか明確にして話を進めたほうがよいでしょう。
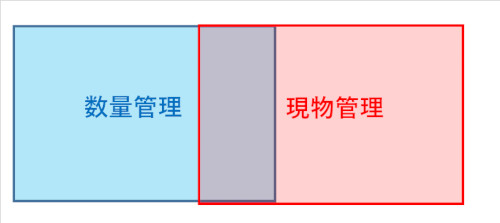
前者は在庫数や受け払いの正確な実施・把握・カウントや管理表の作成、製品の品質を適切に保つ保管環境や仕組み構築・運用、安全な環境を維持し倉庫運営するという在庫の現物管理にかかわる業務です。一般に物流部門やそれにかかわる会社が担当します。
後者は、需要動向にあわせて製品や部材が欠品しないよう適切な在庫を発注・維持管理するためのマネージメント業務です。これは在庫数量をどれだけ持ち、どのように発注計画を立てるかという業務になります。一般に、生産管理や購買管理の業務となります。
ここではこれらを踏まえ、在庫という切り口での課題やその背景にある基礎知識、在庫運用のコツ、技法・用語の解説を行っていきます。
在庫管理の仕事内容と基礎的なやり方
在庫管理のうち、需要に合わせて適切な在庫数量を確保して運用していくという業務については、極論すると以下の10項目が実際にやることになります。
- 1.今現在のたしかな在庫数を把握する
- 2.出荷予測を把握する
- 3.品目ごとに保有する基準在庫を決める
- 4.在庫と出荷予測、基準在庫から補充させる入荷量を決めて発注する
- 5.入荷が正しくなされたか確認する
- 6.出荷実績を入力して現在の在庫がわかるようにする
- 7.出荷予測の更新情報が入ったら在庫表に記入し在庫が持つか確認し不足するなら追加発注を行う
- 8.在庫分析を行って一定期間で基準在庫が現在の基準でよいか確認し更新する
- 9.不動在庫・不良在庫・膠着在庫を処分する
- 10.不動在庫・不良在庫の発生メカニズムを明らかにして未然防止に努める
一方、倉庫内における現物管理にかかわる在庫管理には、以下のような業務があります。
- 1.受け払いを正確に実施し正しい在庫を記録する
- 2.受け払いの情報の動きと現物の動きを正しくまわるよう整備する
- 3.製品ごとの品質維持に必要な保管条件にあった環境を維持する
- 4.先入れ先出しを徹底する
- 5.棚や置き場の管理のルールを作り運用する
- 6.倉庫内の安全管理
在庫の数量管理については、システムで行っているところも多いですが、エクセルファイル1つあればできます。コツとしてはなるべく時間をかけずに必要な情報だけを集め、在庫、入荷、出荷の正しい数量を把握することが第一となります。
またミスを検知する仕組み、例えば合計数があわないといったことがエクセルでわかるよう計算式を入れておくのも有効な方法です。検算を毎度エクセルで自動で行えるようにし、手動計算や目視での照合は、工数の面からも正確性の面からもなるべく避けたほうが無難です。
多くの在庫管理者は大量の品種や製品、部品、材料の管理を一人で行いますので、一覧で管理できる在庫表を作ることが効率的な業務につながります。エクセルで作る在庫管理表のフォーマットの一例は別途ご紹介します。
各社でどのタイミングや順番でやるか、どの部署がやるかというのは違いはあると思いますが、上記の内容をカバーできていないと在庫が欠品したり過剰在庫となって倉庫に置き場がなくなったりします。したがってこれらが在庫管理の基礎とも言えます。上記の10項目からさらに派生して付加業務を行ったり、その一部や大部分を自動化して人が仕事として行う部分のウェイトを「判断」に重点を置いていくケースもあります(規則性のある単純作業の自動化)。システムで管理するとデータの打ち間違えやポカミスなどヒューマンエラーによるミスを防げる利点がありますが、導入には費用がかかるため、ある程度の在庫規模がないと難しいかもしれません。
分野別の在庫管理の仕事内容
在庫管理は大きく2つに分かれると述べた通り、倉庫内の在庫の現物管理にかかわる業務と、適正な在庫数を維持し運用する在庫管理業務をまとめると下表の分野があります。現物管理に関する仕事は倉庫運営業務と密接なものもあり、厳密には「在庫」に関する業務ではないものもあります。
在庫数量の管理 | 現物在庫の管理 |
---|---|
|
|
在庫管理は利益にどのように影響するか
なぜ在庫管理が重要かといえば、在庫は顧客との取引において納期を守るためということの他、企業経営において在庫は、「流動資産の中の棚卸資産」となり、会社の業績を大きく左右することもある勘定科目となるためです。
企業の儲ける力を示す指標の一つであり、各社が有価証券報告書等に記載し目標値も掲げているROA(総資産利益率)は、より少ない資産(資本)でどれだけ利益を出すことができるかを見えるようにするものですが、以下の計算式で割り出されるため在庫が圧縮されると、ROAも上がることが分かります。
- ROA = (利益÷総資産)×100
つまり、同じ利益なら資産の一つである在庫が少ないほうがROAは高くなります。逆に言うと、利益が同じなのに在庫だけ増えると、ROAが悪化し、その企業は資産(資本)を効率的に使って利益を出す力が低いということになります。
もちろんこの単一指標だけでは企業の持つ稼ぐ力の判断は困難ですが、極論すると株主目線でいえば、ROAの低い企業は「投資した金額をうまく使うことができない企業」であるため、株式を購入し投資する価値があるのか疑問が出てくるということになります。利益を生み出すためにやたらと資金を食う燃費の悪い会社ということになってしまいます。
貸借対照表での在庫
在庫は利益を生み出す元だという主張もありますが、たしかに会計上、会社にどれだけ資金やモノがあり借入がどれだけかを表わすバランスシート(貸借対照表)では現金化しやすい「流動資産」に分類されてはいます。
ただし、在庫が現金になるには実は意外に長い時間かかることが少なくありません。たとえば、同じ流動資産の現金・預金はすでに現金化されているので、いつでも他の経営資源に割り振りできます。設備投資や研究開発に使うこともできますし、新たな事業を開始したり、人を採用して組織を強化することにも使えます。
同じく、売掛金も不良債権化していなければ、一定の期間が経てば現金になることが分かっているものです。有価証券も特殊なものでない限り現金化しやすい部類です。
これらに比べて、在庫は実は売れるかどうかは確実ではありませんし、膠着在庫となってしまうリスクが常にあるうえ、先払いや現金取引でない限り販売されてから売掛金となり、それらが現金となるにはさらに時間がかかります。
すぐに売れる製品であれば現金化しやすい在庫で、流動資産と胸を張って言えるのでしょうが、実際には製品ごとにかなり違いがあります。在庫が増えるとキャッシュフローが悪くなるという言い方がなされるのは、在庫が増えると現金化される速度が落ちるためです。
また過剰な在庫はバランシートの上では固定資産にも影響する場合があります。というのも、在庫の置き場を確保するために倉庫を取得したという場合は、固定資産が増えることになります。
さらに在庫を購入した場合、買掛金が上がります。在庫を購入するには資金もいりますので、借入金が増えます。買掛金や借入金が増えれば、負債が増えますので自己資本比率が下がってしまいます。自己資本比率は返済の必要のない資本の割合であるため、他人資本の影響の受けやすさがどれくらいかを判断する一つの指標であり、つまり経営の安定性を表わす指標としても使われます。
在庫管理がきちんとできず在庫が過剰となることで貸借対照表ではこれだけの悪影響が発生します。
損益計算書での在庫
一定期間のうちに会社がどのように資金を使ってどのように儲けたのかは損益計算書(P/L)が使われますが、ここでも在庫が増えると悪影響が見て取れるようになります。
在庫が増えると、倉庫の賃貸料や管理費、トラックでの輸送費、倉庫管理の人件費といった費用が、販管費(販売費および一般管理費)として増加していきます。同じ売上や利益であれば、こうした販管費が増えると、営業利益が減ってしまいます。
さらに在庫が膠着してしまって売れる見込みがなくなった場合、処分する必要が出てきます。この費用は特別損失として損益計算書に上がってきますので、純利益も減ってしまいます。
キャッシュフロー計算における在庫
キャッシュフローへの影響に少し触れましたが、さらに詳しくみていくと、キャッシュフロー計算書は、入ってきた現金と出ていった現金を、営業活動によるキャッシュフロー、投資活動によるキャッシュフロー、財務活動によるキャッシュフローの3つに分けて記述したものです。資金繰り悪化による黒字倒産を防いだり(利益が出ているのに手元に現金がないために倒産)、粉飾が難しいことから資金調達(融資)の評価に活用されることもあります。
キャッシュフローにおける在庫増による影響は次のようなものがあります。
まず営業キャッシュフローで、棚卸資産の増減額に計上されます。前期よりも在庫が増えた場合、資金を在庫に投下したことになるので、マイナスとして計上されます。キャッシュフローの悪化要因となります。
投資キャッシュフローは有価証券を取得した場合や土地建物といった固定資産・設備投資に使った現金の流れや売却した流れを示しますので、倉庫を新たに購入したというような場合、投資をしたことになるのでマイナスになります。
財務キャッシュフローのほうは、借入金や社債の返済、株式・社債発行、配当実行、資金の借り入れといった現金をどのように調達したか、支払ったかを表します。在庫を購入するのに借入金を増やせば、現金が増えるのでプラスになります。
このキャッシュフローではいかにキャッシュ化速度を上げるかというCCC(Cash Conversion Cycle)の向上と、自由に使える現金となるフリーキャッシュフローを高めることが重要となります。フリーキャッシュフローは、営業キャッシュフローと投資キャッシュフローの差になりますので、在庫が増えて倉庫も買ったとなれば、その差は小さくなり、自由に使えるキャッシュが手元に残らないことになります。
- フリーキャッシュフロー = 営業活動によるキャッシュフロー − 投資活動によるキャッシュフロー
- フリーキャッシュフロー = 営業活動によるキャッシュフロー − 設備投資額
これは投下された資金が本業できちんと回収できているかを示す指標でもあります。
それでも在庫を持つ目的
ただ一方で在庫を大量にもって運営するタイプの企業もあり、そうした企業でも業績が良いケースもありますが、在庫を持つことの本質は「顧客注文に対して欠品させないこと」にあります。事業戦略の観点からも必要なのであれば在庫は持つ、ということになります。ただしあくまで市場や需要にあわせた在庫をもつことが求められます。
言い換えれば、「欠品させることがない」ならば、在庫がないに越したことはありません。それができないから在庫をしているだけです。あるいは欠品したとしても顧客に待ってもらうことができる、待ってもらえる期間中に製品の補充ができるという条件であれば、在庫は不要となります。業種によっては、欠品させる確率である欠品率を何パーセント以内にするという目標があるのでそれにあわせて基準在庫を持つということもあります。
在庫管理はリードタイムが肝
こう考えると、材料調達、生産、梱包、出荷、納品にいたるまでのリードタイムが市場や需要にあわせたものになっているのであれば、在庫はそもそもほとんど要らないということになります。
例えば注文から3か月後の納品で十分な製品であれば、注文を受けてから材料を調達し生産し、出荷、納品がこの3カ月以内におさまっているのであれば、何一つ在庫がいらないことになります。現実的には、注文から納品までの期間は特殊な工業製品であっても短くなる一方で、例えばジャストインタイム方式で必要な分だけ生産することで名高いトヨタであれば、前日に部品メーカーに発注して翌日に部品が納品される、というパターンが多く、中には当日注文が入り当日中に納品という場合もあります。こうなると部品側は注文が入ってから材料準備や生産をしていたのでは間に合いません。
カギは未来在庫を読むこと?
製品の種類や業界によってこの辺りの慣習や運用方法には違いがありますが、根っこの部分にはそう違いはありません。現在の市場動向、顧客需要というのは「読み」がますます難しくなっており、変動も激しいのが常です。一方で、材料調達から生産に掛かるリードタイム、出荷・納品にいたるまでのサプライチェーンを鑑みると、日単位で変化する需要動向を見て生産に掛かったのでは間に合いません。
モノづくりにおける技術革新はかなり進歩しても、材料調達・輸送の部分は依然一定のリードタイムが必要で、特に製造業の場合、工場の生産ラインに材料が投入されてから実際に製品を作っている正味時間というのは生産側が確保しているリードタイムの中の時間でいえば数パーセントにも満たないという検証結果もあるくらいです。こうしたリードタイムが必要なため、倉庫であったり、工程内であったり要所要所で在庫が必要となります。とはいえ、それを無制限に増やしたのでは利益を圧迫して事業活動が成り立たなくなってしまいます。
無在庫での生産ができるメーカーもありますが、原則、それは材料や部品サプライヤーに在庫を代わりに持たせて転嫁している部分が多々あり、それができないところは安全在庫や回転在庫をもって運用する必要があります。
こう考えると材料・部品などの調達契約時にリードタイムについて取り決め、それを短縮することの在庫に対する影響は非常に大きいことが分かりますが、多くの企業ではこの仕入先との契約を担う購買部門・調達部門は在庫管理を行っていないため、安くければリードタイムがかかっても仕方がないというような運用がなされてしまうこともあります。
在庫が多すぎるデメリット
こう考えると在庫は潤沢に持っておいたほうが有利と見えるかもしれませんが、在庫を持ちすぎることのデメリットは下記のように枚挙にいとまがありません。
- いつまで何個売れるか分からない為、客先注文終了によりすべて損失となる(製品コスト+廃棄処理コスト+環境負荷も)
- 品質劣化の懸念
- 保管場所が増大、保管費や管理コストが増大
- 倉庫が過密状態で荷崩れなどの安全上のリスクがある
- 倉庫の出し入れに輸送便が増えて物流コストが上がる
- 品種が増えすぎてしまい、リフトやオペレータの人数が足りなくなる
- 棚卸の手間・工数増大、ミス・不一致の懸念
かの有名なトヨタの大野耐一氏も、効率的な生産の代名詞ともいえるトヨタ生産方式を適用させる前提として、7つのムダの排除を唱えており、その中には在庫のムダが挙げられています。ちなみに7つのムダとは、以下となります。
- 1.つくりすぎのムダ
- 2.手持ちのムダ
- 3.運搬のムダ
- 4.加工そのもののムダ
- 5.在庫のムダ
- 6.動作のムダ
- 7.不良をつくるムダ
この生産方式ではムダの最たるものは「つくりすぎのムダ」であり、これが他のムダの発生源にもなることが示唆されていますが、在庫は少なければ少ないほどいいという前提があります。ただし在庫がないことで生産を停滞させたり、顧客の注文にこたえられないという状態にするわけにはいきません。
欠品がなければ在庫は不要
在庫管理は、「(許容される欠品率の範囲内で)欠品させない」という条件を満たしつつ、最小の数量を目指すことが目的ともいえます。
そうはいっても、実務の在庫管理者の目線では欠品防止が優先となり、手間のかかる管理も限度があり、出荷数量予測の精度にも難があるため、在庫は多めに持つというところが多々あるかと思います。
また在庫増というのは場所があふれかえっていない限りなかなか問題が顕在化しにくく、帳簿で上がってくる棚卸資産に対して経営層、管理層がかなり関心をもって圧縮していこうという強い意志を示さない限りなかなか前には進みづらいテーマでもあります。
在庫管理の流れ、4つのポイント
このために、在庫管理においては何が必要かといえば、ごく単純化すると次の4つに集約できます。
- 1.入荷数・出荷数・在庫数は品目ごとに正しくタイムリーに把握・予測できているか
- 2.欠品率に応じた基準在庫設定は正しいか
- 3.安全上・品質上・環境上で問題となる保管方法や運用方法を行っていないか。
- 4.上記が経営資源(人・モノ・金・情報)の面から最も効率的にできているか
1.入荷数・出荷数・在庫数は品目ごとに正しくタイムリーに把握・予測できているか
入荷数とは生産計画や仕入先への発注と連動しており、発注した数がきちんと入っているかを管理することになりますが、そもそも対応できないような数量を発注すると仕組みが成り立ちませんので、工場の実情を把握したうえで行うことになります。
出荷数とは、客先への納入であったり、次工程にある工場への納入であったり、倉庫から出荷される数の予測と実績を管理していくことになります。予測は、客先発注の内示を使ったり、自社の営業が予測する売上予測を使ったりすることになります。
在庫数は、前の在庫に入荷を足して出荷を差し引くことで計算上出されますが、もとの在庫が間違っているとすべて数量が狂ってしまいます。実棚と呼ばれる実地棚卸を精度よく実施することで在庫はきちんとみえるようになりますがこれにはコストがかかるので、なるべく実棚せずに精度のよい在庫数を管理する仕組みを構築する必要があります。
在庫数が正しく把握できること、がまず一番重要になります。これが間違っていると、適切な入荷や出荷を想定したところで欠品や過剰在庫の山となってしまいます。 在庫がきちんと計上される仕組みができてから、出荷予測の精度を上げ、基準在庫を決めて入荷計画を作っていくという流れになります。
2.欠品率に応じた基準在庫設定は正しいか
基準在庫とは、倉庫にある製品をどれくらい在庫しておけばよいかの基準となります。絶対数で例えばこの製品は常時1000個を下回っていけない、最大は1500個以内にしないといけないといったものから、次月の内示や数量予測に対して、3日分の在庫数量を持つ、というようなものまで在庫を持つ基準を決める必要があります。
10%の確率で欠品してよいのであればそれに応じた在庫を持つように基準在庫を設定することになります。
在庫管理とは、この基準在庫を維持するよう精度の高い出荷予測情報を集めて、入荷計画を作ることでもあります。カンコツで決めてしまう職場もありますが、適正な基準在庫には根拠があるべきもので、理論的な裏付けがあってはじめて成り立ちます。
基準在庫は最低在庫と最高在庫の双方を設定してその範囲に収まるようにするのが一般的です。というのも入荷直後は在庫が跳ね上がって増えますが、入荷直前は基準在庫ぎりぎりまで在庫が減ることになるためです。どちらか一方しか設定していないと欠品のリスクが高まるか、過剰在庫のリスクが高まります。
基準在庫には安全在庫も入っており、企業によっては基準在庫=安全在庫のことと定義されていることもあります。
仮に持つべき在庫の基準を必要な日数分で管理するとした場合、次月の需要に対して何日分の在庫を持つべきかという基準在庫に何を加味するかというのは各社の個性や考え方が出る部分で、業界の納入慣習や受発注の仕組みも影響します。具体的には以下が影響してきます。
仕入先・工場への在庫補充
- 発注と納入は定期か不定期か
- 発注してから入荷までどれくらいかかるか
- 発注数量・納入数量の単位は
- 発注は内示とどれくらいの振れまで許容できるか
- 遅延はどの程度発生するか
客先からの受注
- 受注間隔はデイリーか、ウィークリーか、あるいはマンスリーか
- 受注してから納入までのリードタイム
- 内示と発注のブレはどの程度あるか
- 欠品した場合、納期調整がどこまで許されるか
例えば、欠品が許されない業界で、サービス率を100%とした場合、以下のような式で基準在庫を設定することも可能です。
- 基準在庫=在庫補充の発注から納入にかかる日数+客先から受注してから出荷にかかる日数+安全在庫
ここでいう安全在庫とは、客先からの注文の振れや遅延などで入荷がない確率を加味した数量のことです。例えば次月は10000個の内示があり、日当たり500個の必要数として最低在庫を4日分の2000個構えていたとします。ところが客先側で急に注文を増やしたいという要望があり、日当たり2000個を引き始めたとしたら、2日で在庫がショートします。ここまで無茶なケースは稀ですが、あるにはあります。
さらに、これが例えば輸送に長大なリードタイムがかかる輸入品であった場合、船便が遅延したり現地工場が出荷遅延を起こしたりした場合にエアー便で挽回することを考えると、その日数を加算する、という考え方もあります。
1週間に1回の入荷で、週間の客先からの注文の振れが内示に対して200%だったとします。上記の次月10000個の例でいえば、1週間で必要な最大の数は、200%×5日=10日分の在庫となります。振れがなかった場合の必要数5日分をここから差し引くと、振れた分として持っておくべきエクストラとなる安全在庫は5日分となります。1週間に1回万が一入荷がなかった場合、エアー便で現地から出荷してもらい入荷するのが7日としたら、以下のような計算式も成り立ちます。入荷したものはその日のうちに客先に出荷できると仮定します。
- 基準在庫=5日分(安全在庫)+7日分(最短の入荷輸送リードタイム)=12日
輸入品としてはかなり際どい基準在庫設定になりますが、こうしたロジックをもとに、品目や品番ごとに基準在庫を設定していくことになります。客先の注文が異なり、作りも異なる場合、やはり品番ごとの基準設定が一番合理的です。
一律20日といった方法もありますが、製品によってはどうしてもこの基準に入らないものが出てきますので、20日で設定したらほぼこの基準は超えてしまうと見たほうがよいでしょう。例えば、日数での在庫管理の弱点のひとつですか、客先への出荷数を予測していた内示が変動した場合には、在庫日数が激減したり、激増することになります。
上記の次月10000個で、在庫4日分、2000個の在庫を維持していたとしても、この10000個が100個になった場合、在庫日数は400日分になります。
またこの基準は不変のものではなく事業環境や市場動向にあわせて変えていく必要があることを付け加えておきます。
3.安全上・品質上・環境上で問題となる保管方法や運用方法を行っていないか。
昨今は多くの企業で共有されている「安全はすべてに優先する」という認識があっても物流倉庫での事故というのは無くなることがありません。オペレータや出入りの輸送業者、倉庫に出入りするすべての人にとって安全な倉庫を構築する必要があります。
品質上とは、FIFO(先入れ先出し)を守り、製品の古いものから出荷していく原則や、温度や湿度管理など製品の特性によって必要な環境を構築・維持することを意味します。
金属製品であれば発錆が気になりますし、温度によって製品が劣化してしまうものであれば、温度管理の仕組みも必要です。
環境上とは環境負荷の高いものを製品の維持管理になるべく使わないという発想です。リターナブル容器の検討や、荷材のリサイクルもその一つの考え方です。
4.上記が経営資源(人・モノ・金・情報)の面から最も効率的にできているか
在庫を多く持つということはそれだけ会社の現金が現物在庫に変わってしまい、それが顧客へ販売されて現金化されるまでにはさらに時間がかかることを意味します。つまるところ、持ちすぎるとキャッシュフローが悪化します。
現金の状態であれば様々な経営資源に投下できる資金が在庫にかわることで減ってしまうわけで、企業が資産をどれだけ有効活用できているかという面でも悪影響を及ぼします。こうした観点から在庫の持ち方を構築・再検証をする業務となります。
- 倉庫の運用や管理にかかるコストの低減(場所、設備、使用機材、管理方法)
- 人の有効活用、省力化、自動化
- 正しい情報(在庫情報、出荷予測、入荷実績)を適切に活用できているか
- 在庫の現物の状況がすぐにわかる状況か
製造業での在庫管理の問題と課題
製品を実際に作る製造業、メーカーにおける在庫管理には他業種にはないいくつかの特徴があります。もちろん共通項も多いので、在庫管理をされている方にとっての「あるある」事例もあると思います。
同一のものであっても材料、仕掛、完成品と在庫場所が多岐にわたる点がまず一番大きな違いです。またそれらは管理者や運用者、管轄が異なることが多いため、自分の担当以外の部分はなかなか見えづらいというのも問題の一つです。在庫低減に取り組む場合、作りの部分や入出荷の動線まで検討していくことが場合によっては有効で、全社的な活動として進めていく必要があります。
生産性を優先すると在庫が増える場合
他業種においても「まとめ発注」によって仕入れ単価の低減に成功して利益率が上がったとする事例は多いですが、これは売れたものだけが利益率としてカウントされるからで、最終的に在庫が売れ残っていつまでも現金化されなかったり、廃却処分されることが考慮されていません。目先の利益率を重視してキャッシュフロー悪化をはじめとする在庫増と膠着在庫に目を向けないとあとで手痛いしっぺ返しを食らうことになりますが、多くの企業では発注を決める部門の評価をこの利益率や仕入れ単価を如何に安くしたかという指標だけで決めており、在庫の膠着やその費用は在庫管理運用部門へ丸投げし、知らぬ存ぜずというケースもあります。
この理屈は工場にもそのまま類似するケースがあります。これは作っている製品の特長にもよるのですが、一度にたくさん製造したほうが効率が良いタイプの生産品で、人生産性、マンアワー生産性で工場の評価を行っている会社の場合、ロットをまとめた生産のほうが金型の入れ替えをはじめとする段取り替えが少なくなり、否が応でも生産性が上がっていきます。このため、必要な分を必要なだけ小刻みに作るという在庫にとっては最も望ましい方法とは真逆の生産方法が取られることがあります。
こうした課題に対しては工場の責任でもつべき在庫と、本来の需要に応じてもつべき在庫の責任をきっちり分けて考えるべきという意見もあります。生産性が高いとは、製造が効率的にできるため、結果として製造にかかるコストが落ちるわけですが、そのために在庫が大量にできてしまって営業サイドにそのリスクを負え、というのは社内軋轢のもとにもなる発想です。
完成品以外の在庫がある
市場や顧客へ納入する製品以外の在庫も対象となる点が製造業における在庫の大きな特徴の一つです。物を製造するには材料や部品を購入しそれらの入荷計画も加味しながら生産計画を立案する必要があります。
さらに製造途中工程における工程内在庫です。生産にかかるリードタイムに応じて、各工程では作り途中のいわゆる仕掛品在庫が存在します。生産のロットやリードタイムによってこれらは変動しますが、出荷直前の検査前のものであっても合格品ではない以上、仕掛品となります。
- 1.完成品
- 2.仕掛品
- 3.完成品を製造するのに使う部品や材料
- 4.製造に使う消耗材・副資材
- 5.製造に使う薬剤、化学物質等
一般に在庫といった場合は、1〜3が対象となり、これらの適正化や低減を進めることになりますが、その結果として4や5も減らすことができます。
- 生産リードタイムや部材供給タイミング等の改善で工程内の在庫をいかに減らすか
- 部材の調達リードタイムとロットをいかに自社で在庫少なく運用できるよう交渉するか
上記が重要となってきます。製造現場においては実際に機械に材料をセットして作る時間に比べると、運搬や保管に費やしている時間が本当に多いです。これらの時間はリードタイムとして加算され、その分を在庫として持っていないとまわらないため、製品になっていない在庫がばかにならないレベルで棚卸時に発覚することもあります。
工場在庫と営業在庫|在庫管轄の問題
工場で完成品に仕上げた在庫を工場側の資産として管理運用するのか、販売窓口となる営業部門の在庫として運用するのかというのは、同じ会社なので大した違いはないと思われるかもしれませんが、組織体制によっては雲泥の差が出ることがあります。
そもそも在庫の持ち方や考え方が工場と営業とでは異なったり、管理監督者の考えひとつで在庫の運用方針は大きく変わりますので、それぞれの在庫管理責任者が違っている場合で、方針も異なる場合、会社としてはかなりちぐはぐな在庫運用がなされることがあります。
それぞれの在庫は往々にして、工場在庫は工場倉庫やその契約先となる外部倉庫を使い、営業在庫は物流拠点やデポといった客先へ納入する一歩手前の物流拠点で扱うという住みわけがなされています。
これは実際にあった事例です。
- 営業在庫を減らしてキャッシュフロー改善に貢献したと営業部門は主張。
- 欠品率が増加し、チャーター便などの輸送費が大幅増となった。この費用は間接部門である物流部門が負担した。
- 客先の納入に間に合わない事態が頻発する為、営業在庫で減った分を工場在庫で持たせる方式に変わった。単なる在庫の転嫁で、会社としては何の変化もない。むしろマーケットの情報から遠い工場側では安全在庫を多く見積もりすぎて、会社全体の在庫はかえって増加してしまった。
また、それぞれの管理責任者のもと、置き場がないので外部倉庫を借りて保管しているという場合も多々あると思いますが、こうした在庫場所が複数に分散されるとそこへの出し入れにかかる輸送費や管理コスト、輸送リードタイム、在庫総数のカウントミスなども課題となります。
在庫区分 | 在庫内容 |
---|---|
営業在庫 | 物流拠点やデポで完成品としての在庫 |
工場在庫 | 自社内のストアや工場倉庫に保管する完成品のほか、検査前品や仕掛品も工程内に保有。また部品や材料、生産に必要な資材全般の在庫も保有。 |
部材で持つか完成品でもつか
客先からの発注から納入までに猶予がない場合、製造業でどの工程でも無在庫というのはなかなか難しいのですが、在庫金額を落とすために、完成品在庫ではなく、その部品や材料の段階の在庫を比較的多めに確保しているケースがあります。
完成品在庫を一定に落とすために部材の在庫が多めになる、というようなことが発生します。これを社内でコンセンサスをとって戦略的に実施しているのであれば何の問題もないのですが、部材の在庫を管理している部隊が、在庫低減に単独で取り組んだ結果、完成品を管理している部隊はいつでも作ることができるという状態ではなくなってしまったため、完成品在庫を増やさざるを得なくなったというケースもあります。
どちらの在庫も減らせればそれに越したことはなく、双方が増えるというのが一番望ましくない結果ですが、この社内での綱引きがうまくいかずに、部分最適ができても、全体最適ができていないので会社全体の在庫はたいして低減できていないということもあります。
在庫場所が複数に分かれてしまう
部材を保管している倉庫と、工場内の工程内在庫で状態が全く同じ在庫が複数存在することがあります。工場は原則使う分だけを倉庫から取り入れ随時使っていますが、製品が大量になると、例えば、1日分を前もって取り入れてしまうだけですさまじい在庫量になることがあります。加えて、1日分を倉庫から工場が取り入れると、倉庫から減った分をまた仕入先に発注して補充する必要があり、在庫が余計に増えます。
これは中継場所が多いほど在庫が増えることを意味しています。
また工場の生産予定が倉庫側の在庫運用者といかに情報連携できているかという点も重要となります。生産計画が部材発注リードタイムにあわせて前もってわからなければ、部材担当者は、生産を止めないよう多めに部材を発注してしまいます。結果、客先の注文が急に減って工場の生産計画が変わると部材は大量に膠着してしまいます。
在庫があわない
在庫の適正化を行うにしても、すべての原点は今カウントされている在庫が正しい数量であるという前提で検討を行いますので、実在庫と帳簿上あるいは在庫表の数量があわないという場合は、まずはそこから正す必要があります。
簡単なようで未経験の作業者や管理者ばかりだとこれが確実にできるようになるまで試行錯誤が必要になります。
在庫があわなくなる代表的な原因を参考までに列挙します。
- カウントの日付がずれている
- 「何月何日の何時に出荷した後の在庫」と決めてカウントしているにも関わらず、出荷前の在庫が計上されてしまっている。
- 在庫置き場が決まっていない、同一品が散らばっている
- 同一の製品の置き場が同じ倉庫内で分散しており、作業者が見落とす。製品ごとで置き場が決まっていない所謂指定席ではなく自由席のように保管している場合、カウントが漏れてしまう。どこに何を置くかの情報共有ができていない。
- 伝票の取り回し方法が曖昧、検算される仕組みがない
- 出庫伝票・出荷伝票をもとに在庫表へ入力する業務形態の場合、伝票置き場間違えや何らかの理由での紛失で出庫が正しく記録されていない。
- 在庫表のミス
- 在庫表の記入ミス。打ち間違い、前月末の在庫がそもそも違っている。計算式を間違えている等。
- 入出庫作業とカウント・データの不一致
- 入出庫のルールやどの時点でカウントするか、カウントすべきものが置かれる場所などに決まりがなく、担当者によって変わってしまう。入庫データが古い、あるいは現物照合される仕組みがないのに関わらず間違った計算上のデータが継続して使われてしまっている。
基準在庫設定、安全在庫が適切か分からない
基準在庫の設定は、いつどれだけの発注が必要かという情報を決める基礎となる部分ですが、運用者の視点では欠品を恐れて多めに設定する傾向があります。設定のロジックの検証が必要で、定期的な見直しも実施することが必要になりますが、なぜその基準在庫になっているか説明がつかないケースが散見されます。担当者の勘で多めにしている、頻繁に段取り替えをしたくないし、手配の急増に振り回されたくないので現場判断で多めに持っているケースもあります。
全体を見る立場の部署や担当が設定に関与すべきです。楽をしたいので、というのは改善の立派な動機ではありますが、それが理由で会社に損失が発生したのでは元も子もありません。現場の意見や勘は時に有益なアドバイスとなりますが、全体を俯瞰する視点も必要です。
毎回在庫が余っているようなら見直してみるのも一考の価値があります。上記の課題ともかぶりますが、製造分野では同じものを複数の場所で在庫するのはよくあることです。ライン側で在庫を持っているなら、その前の倉庫での在庫を減らして、トータルでどれだけの在庫を持つ必要がある、というロジックをたてて運用することが大切です。
実在庫が基準在庫、安全在庫から乖離している
担当者の独断やカンコツに頼りがちな運用方法であればその可能性もありますが、多くは、決められた基準在庫・安全在庫になるように狙って発注業務を行っているにも関わらず、在庫が過多になったり過少になったりする現象です。
これは適正在庫になるよう狙って正しい数量を発注しているにもかかわらず起きる場合もあり、その典型例が内示の変動です。次月の出荷予測にあわせて在庫を設定しますので、それが大きく外れてしまえば、今の在庫が〇日分という指標そのものが大きく狂ってしまいます。
こうした変動要因だけでなく、ロットが大きく基準在庫にあわせられない、遅延が頻発して入荷時期がずれる、不良が多発して良品の個数が読めないといったことも乖離の原因となります。
以上、在庫管理の定義から仕事内容、在庫の増加による利益への影響、業務の流れや抑えておくべきポイント、製造業やメーカーの在庫管理に固有の課題・問題等、在庫にかかわる基礎知識をなるべく網羅的に説明してきましたが如何でしたか。以下に具体的な個々の課題についての記事も紹介していきます。
在庫管理に関する記事一覧
- 棚卸に必要な英語表現|実地棚卸立会から棚卸票、英語での在庫用語
- 英語で品質保持期限は何というか
- FIFOとは|先入先出における在庫管理
- 製造や生産におけるFG、WIP、RM、SFGの意味|完成品、仕掛品、半製品、原材料を英語で言うと
- 自動車部品や工場でいわれるストアとは何か
- かんばん枚数の設定・計算方法|かんばんサイクルの1-1-1や1-1-2の意味とは
- ライン側、「ラインそく」とは何か
- パレタイズコードとは
- 段取り替えの意味、その改善方法とは
- 内示とは|発注や注文における内示情報を製造で活用
- 廃却証明書のフォーマットと英語テンプレート|廃却証明書はなぜ必要か
- レスターの意味とは
- 在庫管理でのエクセルテンプレート
- 在庫の横持とは
- シェルフライフの意味とは
- 在庫における粉飾とは
- 在庫金利の考え方と計算方法とは
- 廃棄と廃却の違いは
- 在庫管理の定義
- 不動在庫の定義とルール
- 在庫の日数はどうやって決める?
- 膠着在庫を英語でいうと
- 長期在庫の定義とは|長期滞留のデメリットと処分方法
- 倉庫における錆対策
- 製品と商品の違い
- 内外作区分の意味とは
- 不動在庫と滞留在庫の違い
- 在庫回転期間の業種別目安と計算方法
- 在庫率とは何か
- 在庫管理における最低在庫、適正在庫とは
- 在庫管理の目的と目標設定
- 在庫にまつわる不正の手口
- 棚卸資産と在庫の違い
- 工場在庫と営業在庫
- 在庫の押し込み
- 商物分離のメリットとデメリット
- 受領書と領収書の違い
- CCCの計算式とは
- 在庫の廃棄ルールについて
- デカップリング在庫の意味とは
- 棚卸における出量、欠量とは何か
- 在庫におけるDOHの意味とは|DOHは英語で何の略語か
- SKUの意味と例
- 納品書控と受領書の違い
- 不動在庫の反対語
- 在庫成り行きの意味とは
- 廃棄伝票とは
- 棚卸におけるテストカウント
- 棚卸対象外の理由表示について
- 棚卸での監査のポイント
- 棚卸における積送品とは
- 預かり在庫証明書の雛形
スポンサーリンク