自動車部品のサプライチェーンの構図
自動車には約3万点とも言われる大量かつ多種多様な自動車部品が使われており、そのサプライチェーンはまさに網の目のように広がり、階層構造をしています。以下にこの自動車部品のサプライチェーンの構造、特徴、課題についてみていきます。
昨今話題となっている、なぜ自動車部品が入ってこない事態が発生し、自動車の減産が発生するのか見ていきます。直接または間接的に関わる会社が非常に多く、裾野が広い産業であるため、自動車工場の稼働状況によって売上が大きく変動する会社の数が多いというのもこの産業の大きな特徴といえます。
取引の形態、支給と下請の嵐
基本構造としては、OEMと呼称される自動車メーカーを頂点に、その直接のサプライヤーとなるティア1から、そのティア1へ納入するティア2、さらにその下請けメーカーなどピラミッド構造になっています。下図の通り、一次メーカー、二次メーカーへと注文が下にどんどん降りていく構造です。
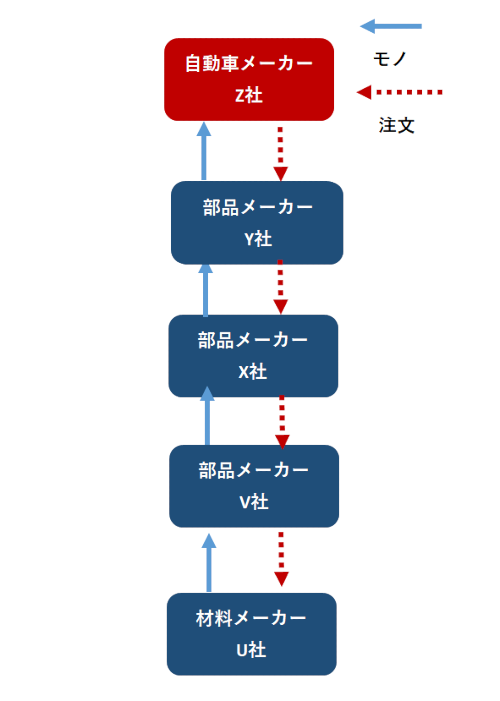
一方、これだけでなく同階層であるティア1同士やティア2同士等でも納入のやり取りが活発に行われる点が大きな特徴です。ティア1→ティア2という取引もあります。またそれぞれで2社間の売買でも支給品も存在するため、取引先と納入先が違うということも日常茶飯事です。こうなると、A社とB社の取引にもかかわらず、実際の部品はC社とD社の間で納入のやり取りが行われるということが起きます。
下図をご覧ください。この例では、部品メーカーA社とB社はどちらも自動車メーカーZ社と直接取引しています。Z社はA社の部品を購入してB社に販売し、その部品を使って完成品に仕上げたB社の製品をZ社は購入します。

一方、実際の品物は部品メーカーA社も部品メーカーC社に作らせており、C社へはA社が購入したW社の部品を有償支給しています。C社はさらに下請先E社を使って製品を作らせています。また自動車メーカーZ社へ直接納入するB社も、部品そのものは下請先となるD社に作らせています。
すると、実際のZ社からの支給部品はC社からD社に納入され、それがB社へ納入されてZ社へ届くという形になります。これが何階層にもなっていたり、さらに多くの部品メーカーや加工メーカー、材料メーカーが国内と海外双方で複雑に絡み合っているのが実際の自動車部品のサプライチェーンの姿です。「有償支給と無償支給の違い、それぞれのメリット、デメリットのまとめ」でも支給品の構造を述べていますのでご参照ください。
なぜこのような複雑な取引となってしまう支給を行うのかといえば、コストダウンや品質維持のためということになります。仕入先となる各メーカーの自達(自社調達品、自家調達品)に任せるよりも、発注元がコントロールするほうが均一な品質を維持したり、大量購入や細かい査定によって有利な購買が可能でコスト面でもメリットが出せるため、ということになります。
ただしこのような複雑な取引にすればするほど、関係する会社の数が増えますので、どこか一社で何かあった場合、それがおおもとの供給に影響を及ぼすという事態にもなります。
すべての組み立てを車両工場で行うわけではない
自動車メーカーでは車両の組付け、つまり組み立てをメインにしており、エンジンやトランスミッションなどのコアとなるものを除くとほとんどが社外からの調達です。部品によっては複数の部品が組み立てられた状態で自動車メーカーに入ることになるため、部品メーカー同士での物品のやり取りが盛んにおこなわれるという実態です。自動車メーカーとの取引で支給元と支給先という関係もあれば、部品メーカーを直接の顧客として取引するケースもあります。
ティア1メーカーの中でも特に大きいモジュールメーカーへ各部品メーカーが納入し、ある程度の大きな塊に組み立ててから部品を自動車メーカーへ納入するという形も部位によってはあります。
支給については部品だけでなく、集購(=集中購買)と呼ばれる「まとめ買い」を自動車メーカーが行い、部品メーカーが単独で買うよりも安く調達して、それを有償で部品メーカーへ支給するという手法も取られます。集購材と呼ばれる鉄鋼材料はその典型です。力の強い鉄鋼メーカーとは部品メーカーが単独で交渉しても価格は下がりませんので、鋼板をはじめとする材料を自動車メーカーの集購材として購入し、自社で自動車部品に加工してまた自動車メーカーへ納入するという形態です。
多回納入が基本、大量の部品が毎日行き交う
使用する部品点数が多いということはそれだけ自動車工場にも部品をストックしておく場所が必要ということになりますが、これだけの点数になると在庫は持たないかライン側にごく少数持つというものが大半を占めないと、早々に工場が部品だけで溢れかえってしまいます。半導体など小さくて特殊なものは在庫していても、大型の部品をはじめ、小型でも大量使用が前提となる業界ですから、必要な部品だけを必要な時間に納入するよう発注がかけられます。
したがって、多くの自動車メーカーでは1日に数回あるいは何度も納入する多回納入形式で発注がなされます。1時間や2時間置きに納入時間と場所が決まっており、そこへ発注のあった分を納入することになります。これはつまるところ、限られた時間内に使う分しか注文しないということです。
これらはかんばんや電子取引の形で注文データを受領する形でサプライヤーが受け取り、指定された時間に納入するか、自動車メーカーが準備するミルクラン便に載せて納入することになります。
ライン停止やサプライチェーンの危機はなぜ起きる
これだけの部品点数があると、どこか一つの部品メーカーからの供給が止まるだけで自動車の車両生産のラインを止まってしまうことになります。いわゆるラインストップです。
これをサプライヤーの要因で行うとペナルティを課す自動車メーカーが一般的ですが、量産ラインを止めるようなメーカーとは取引を基本的に行わない傾向があります。したがって量産ラインに対しては納期遵守率100%が原則です。
様々な供給リスクが発生しても、どのサプライヤーも自社の責任で客先となる自動車メーカーのラインを止めることはしたくないため、ときにはコスト度外視で納入をつないでいきます。ただしこれは部品メーカーと自動車メーカーとの力関係や商習慣にもよります。
例えば、自動車メーカーの多くの減産要因になった半導体供給不足問題は、もともと半導体のメイン顧客は自動車ではなく、優先的に回ってこないという問題や半導体部品の商取引の慣習から、自動車メーカーがある程度の在庫を保有しています。通常、自動車メーカーは部品メーカーに対して納入時間指定で発注する為、在庫等ほぼ持たないのですが、このように部材によっては異例の対応を行うことになります。
また外資系の部品メーカーは日本固有の商習慣や馴れ合い的なものを嫌い、契約に則って取引を進める傾向があり、自動車メーカーの突発的な無理難題に対しても「無理なものは無理」というスタンスを通すところもあります。日系部品メーカーによっては自動車メーカーからの突発依頼や緊急依頼に対しては時に採算度外視で応えることもあります。
昨今は日本だけでなく世界中から部品を集めてくることになり、例えば日本生産の部品でもその部材は複数の国から輸入しているということも珍しくありません。このため、自動車のサプライチェーンにおいてはグローバルな視点が常時求められます。
どこかで供給に影響する問題が発生した、寒波での大規模な停電が起きた、原材料メーカーや部品メーカーでの火災が発生した、材料メーカーがFM宣言を出して供給を断ってきた、材料が別業界に回って優先的に確保できなくなった、自然災害が起きた、コロナでロックダウンした、水害が起きて工業団地が水浸しになった、輸送網が寸断した、コンテナが不足したとなると、部品供給リスクが発生することになり、各サプライヤーへの影響調査も実施されることになります。
前述したようなリスクでひとつの部品でも入ってこず、車両が作れないということになれば、そこで自動車メーカー側では生産計画な見直しや入荷めどが立つまでの間大幅な減産となります。使用される部品が多く、調達先が多岐にわたるために、世界中の様々な情勢がダイレクトに影響してくるようになっているというのが実情です。
同一部品を複数の工場から同時期に供給することができない
これは業界で働く人にとっては常識となってしまっているためあまり気にもされていないのですが、あるモデルの車に使われている固有の自動車部品は、必ず1つの工場の量産工程で作られているもの、ということになります。
たとえばあるサプライヤーでは、世界にあわせて10の工場を持っており、そのうち5工場で、A部品を作ることができる、としましょう。この場合でも、日本の自動車メーカーにA部品を納入する際、その自動車メーカーの日本工場へ納入が許可されるのはあらかじめ決められている1工場だけで作ったものということになります。その自動車メーカーの海外工場に対して、最寄の海外工場からA部品を納入するというのはもちろん可能ですが、この場合も、申請した1つの工場以外で作ったものを納品するのはNGとなります。
これは品質管理の観点から定められているルールで、同じ材料、同じ設計、同じ製法であっても、生産する工場を変える場合は自動車メーカーへ工程変更の申請を出し、評価を受け、承認を経てからでないと変えることができないというものです。
このため、量産されている自動車工場にまったく同じ部品が同一メーカーの複数工場で作られるということは特別な事情がある場合を除き原則として存在しないということになります。
上記からお気づきかと思いますが、こうしたサプライチェーンだと災害が発生してそのサプライヤーの工場が被災した場合、一気に供給不安が発生するということになります。同一工場という縛りがあると地理的に分散できず、平時は一カ所の工場のみでの生産になります。
さらにいえば、自動車部品は複数の車種、同一プラットフォームを持つ車種に流用される傾向があります。これはコストを抑えるための工夫ではあるのですが、多数の車種にグローバルで使われている場合、その部品を供給するサプライヤーが1工場で対応しておりそこに何かあった場合、全世界でその部品が使用されている車種の生産が止まる、ということになります。
バックアップ体制
あらかじめ申請してある工場で作ることができなくなった場合、自動車メーカーへ申請することで(同一のスペックであるというデータでの証明ができる前提)、別工場で作ったものを納入することもできますが、複数の別工場で作ったものをかき集めてミックスして出荷する、ということはできません。また、今日はA工場で作ったものを納入、明日はB工場、明後日はまたA工場というようなことも原則できません。
コロナ禍で操業がストップしてしまった工場にかわり、自社の別の国にあるグループ会社で生産し自動車メーカーのラインストップを回避するという動きも活発に行われましたが、半導体のように生産台数減を余儀なくされたケースや、原料メーカーによるFM宣言に端を発して生産ができなくなる部品等が頻発しました。これらは代替生産ができなかったケースの典型例です。
何か事故や不測の事態が起きると部材調達や供給に問題がないか一斉に調整依頼が飛んでくるのもこうしたサプライチェーン網に綻びがないか、ある場合すぐにバックアップや代替方法の検討ができるようにするためでもあります。
集中購買の原則
生産できる工場が限定されているということからもお分かりかと思いますが、同一の車種や車型では必ず同じメーカー・同じ工場で作られた部品が使われているということが原則になります。したがって、1社で何かトラブルがあったので、同一部品を作っている別メーカーへの発注を増やして対応というようなことが臨機応変にはできません。稀に、深刻なトラブルが発生した場合は、一時的に競合部品メーカーへ緊急対応依頼(立ち上げから納入まで通常のリードタイムよりもはるかに短納期で対応する案件)が来ることもあります。
ただ自動車部品が量産で使えるようになるまでには2年近い歳月をかけて評価を実施した結果であり、すぐに切り替えるというのがなかなか難しい世界です。部品としては供給できても車両に組み付けて見たら、不具合が出てきたとなると市場対応案件にもなってしまいます。とにかく評価の時間がまったく足りないという環境での切り替え・代替生産のため、どのような不測の事態が起きるか不透明という問題があります。
品質の問題とコストの問題から購入先がある程度絞られており、この車種のこの部品はAサプライヤーにするというような形態がとられているので、そのAサプライヤーで何か起こると、上記の事態を引き起こします。
また同系統の自動車部品というのは、素材が全く違うというのはなかなか珍しい部類で、素材となる原料メーカーが世界に1社〜数社しかない、というケースも多々あります。複数社あっても購入できる先が一社しかない場合、そのメーカーからの調達が途切れてしまうと、その材料を使用している部品メーカーが根こそぎ生産停止となってしまいます。
集中購買はコストを下げるというメリットがある一方、リスクの分散という観点からは課題が残ります。
BCPの取り組み
BCPとは、事業継続計画(Business Continuity Plan)のことですが、自動車業界で使われる場合、部品メーカーに対して災害や事故、不可抗力となるような現象が発生して部品の供給ができなくなった場合、どのようにしていつまでにバックアップしてくれますか、という調査依頼のことでもあります。
自動車メーカーの調達担当が部品ごとに調査依頼をかけて定期的に更新を行っていますが、実際にそうした事態に遭遇したメーカーでないといまいち実感もわかず、大規模な災害が起きた場合は本当にバックアップできるのかという懸念もあります。
基本は、同等の能力を持った別工場での生産か、在庫で対応、在庫を複数の場所に分散するというような対策になります。あとはどの程度で復旧できるかという目途を記載することになりますが、これは損壊の程度によりけりで、試算をしても実際に発生した場合はその通りにならない可能性大といえます。
結局、BCPの観点から調達不安のリスクをいかに減らすかという試みも、昨今のFM宣言や半導体の状況を見ればお分かりの通り、万能ではありません。それどころか、実は特定のメーカーに何かあった場合は、在庫で対応する以外に方法がないということが露呈した状況です。
サプライチェーン網が広範になり、世界中の様々なリスクの影響を受けるようになったとはいえ、そもそも同一品を複数社から購入したり、二社購買にしてリスクを分散というのが難しい業界です。また、仮に車種違いで同一分野のメーカー複数社と取引していたとしても、その原料や材料のメーカーに何かあると同じことが発生します。
原料部分を自国のメーカーにする等の対策をとるのは、政治的な理由、地政学的な理由での供給リスクを減らすという意味合いもあります。
品質を維持しながら調達を分散できる仕組みや、工程変更を迅速・簡便にできる方法、情報をいち早くキャッチして供給が止まる前に代替先での生産・出荷を開始できる体制づくりが求められることになります。
スポンサーリンク
「自動車部品のサプライチェーンの構図」の関連記事
- 部品共通化のメリットとデメリット
- 自動車メーカーの稼働停止の影響
- 自動車部品業界の特徴|今後と課題、仕事内容について
- 自動車業界でのCASEとは|CASEの意味とその影響について
- 工程変更とは何か|自動車部品業界における工程変更申請が必要なケース
- 設変とは|ECIにおけるメジャー設変とマイナー設変
- 自動車部品における通い箱|通い箱の規格、サイズ、種類など
- 量産移管の意味と英語表現
- 自動車部品の生産終了や生産中止はどのように決められているか
- FM宣言とは|フォースマジュールの意味
- トヨタの集購材とは
- モノ情の書き方|トヨタにおける物情とは物と情報の流れ図
- かんばん枚数の設定・計算方法|かんばんサイクルの1-1-1や1-1-2の意味とは
- 三発内示とは
- トヨタ生産方式の「物と情報の流れ図」における記号一覧
- トヨタにおけるかんばんの種類
- 自動車の部品はどこで作られているのか
- 自動車の海外生産におけるメリットとデメリット