ガラス研削・研磨用ダイヤモンドホイールについて
ガラスの研削・研磨や切断にはダイヤモンド砥石が多用されます。対象とされるワークは、通常のソーダ硝子から光学ガラス、石英ガラスなど多数の種類があり、ガラスに含まれる物質によってその性質も多様です。おおむねガラス全般に共通する特徴として、硬く脆い材料であり、切り屑が粉状となる、チッピング(欠け)を起こしやすいなどが挙げられます。
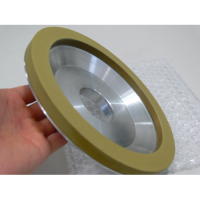
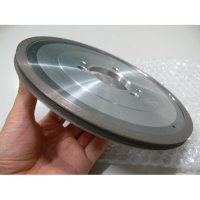
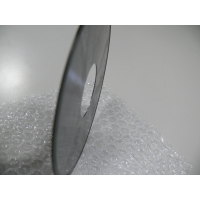
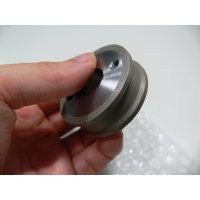
ガラス研削用砥石の特徴と仕様
ガラスの研削・研磨でよく使われる工程
ガラス研削、ガラス研磨は加工する形状により使う砥石も複数パターンあります。板ガラスやその応用製品用としてストレートからカップホイール、切断砥石、軸付砥石まで各種市場には流通しています。
- 切断用:1A1SS型、1A1S型、1A1R型
- 平面研削用:6A2型
- 平面ラップ用:12A2型、11A2型
- 穴あけ用:コアドリル型
- 面取り用:6A2型
- 軸付砥石(電着、メタルボンド等)
粗工程 | 中仕上げ | 仕上げ |
---|---|---|
○ | ○ | ○ |
ガラス研削のための砥石の標準仕様
寸法 | 粒度 | 結合度 | 集中度 | ボンド |
---|---|---|---|---|
各種 | #16〜#8000程度 |
P(硬め仕様) N(標準硬さ) L(軟らかめ) |
標準では60 (10〜150) |
メタル (稀にレジン) |
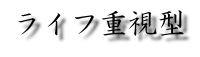
砥石の寿命を重視する場合は、一粒のダイヤモンドになるべく長く仕事をしてもらう発想もあります。結合度を上げて砥粒の脱落具合を調整する考え方です。砥粒にかかる負荷を低減するため、切れ味や目詰まり具合を見ながら集中度を調整することがあります。
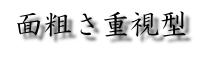
仕上げでの面粗さを重視する場合は、粒度の影響が多いですが、切れ味を後半で低下させ、きめの細かい面が出るよう調整するという考え方です。表面が適度に目詰まりすることで砥粒の突き出しと切り込みを低めに抑える必要があります。同じ粒度であってもボンドが違えば面粗さは変わってきます。
研削条件と、現行品の仕様・問題点などが分かれば砥石メーカーによっては対抗品の選定がスムーズにできる場合もあります。重視する部分の優先順位と、実際に加工したときの条件などをメモしておくことをおすすめします。
スポンサーリンク
ガラス研削の特徴
ガラスの研削・研磨にあまり馴染みのない方には意外かもしれませんが、ガラスは割れやすいのに反し、硬さは非常に硬い材料の一つです。このため、最も硬い物質であるダイヤモンドを使った砥石が多用されています。
硬ければ硬いほど削りやすいといわれるダイヤモンド砥石の性質とガラスは相性がよいです。ガラスの研削・研磨では、ガラス角や板ガラス淵部分の面取り・糸面取りや、板の淵を曲面に加工するペンシルエッジ加工(建材用や自動車用など)、ガラス端面の研削・研磨などが一般に多いとされます。
ガラスの性質上、またガラスを加工する機械や加工量などにもよりますが、メタルボンドを用いたダイヤモンドホイールが加工条件にマッチすることが多いです。狙っている仕上げ面の状態によってはレジンを後工程で投入するなどの考え方もあります。
ガラス研削にはメタルボンドが多用
メタルボンドは金属をベースにした結合材で、砥粒であるダイヤモンドをしっかりつかんで保持します。粘りがあり硬い金属の特性を活かしたボンドは、ガラスの切り屑で削られ、うまく切れ刃が生え変わります。砥石の色でもあるボンドの色は、配合されている金属の比率によって変わってきます。
切れ味に主眼を置いた設計では、レジンボンドを用いたダイヤモンドホイールもあります。ただ砥石のライフという観点からみると、より一枚あたりの加工が低コストですむ寿命重視型をよく目にします。
ガラス研削用の砥石は金属加工用などに比べて集中度が低め
ガラス研削においては、他のワークと異なり、ガラス表面はダイヤモンドが滑りやすいという特徴があります。ガラス研削用のホイールでは、超硬や金属系のワーク用のものより、集中度を下げる、つまり砥石の中に含有されるダイヤモンドの量を減らすことでこの問題の解決をはかっています。
生け花の剣山と同じ原理で、切れ刃となるダイヤモンドの量が減れば、一つのダイヤモンドにかかる圧力が増え、同じ圧力であっても、より深くワークに切り込んでいきます。これにより、ダイヤモンドホイールがガラス表面を滑ってしまう現象を抑えていきます。お使いの機械や研削条件、ガラスの種類によっても変わってきますが、集中度は50〜60前後に設定するパターンが多いです(集中度100で砥石の25%がダイヤモンドになります)。反面、チッピングが問題となる場合や、対象のガラスが硬すぎる場合、集中度を上げていく考え方もあります。
ガラス研削・研磨に使われる研削液(切削油)はほとんどが水です。これはガラスに油が残留してしまってはいけないことや、研削油の処理の問題もありますが、そもそもダイヤモンドが表面で滑りやすいガラスのような材質の潤滑性は極端に上げないほうがよいとの見方もあります。通常、摩擦係数を減らし、法線抵抗をある程度減らしたほうが「切れる」といわれますが、これはワークによります。滑りを抑えたほうがより「切れる」場合もあります。
ガラス研削における問題点
ガラスの研削や研磨を行なう際に起きる問題点についてまとめました。
- フランジの振れ:タタキ現象が起きる→加工物の割れにつながります。
- 砥石軸の振れ:砥粒の軌跡が不安定→砥粒の脱落につながります。
- 平坦度の悪い砥石:タタキ現象が起きる→加工物の割れにつながります。
- 動力不足:研削ホイールの周速の低下→砥粒の脱落につながります。
- 研削液・研削油の不足:発熱→砥石の目詰まりにつながります。
- 砥石の周速が速過ぎる→砥石の目つぶれにつながります。
- 砥石の周速が遅すぎる→砥石の目こぼれにつながります。
ガラス研削(面取り加工)の一般的な研削条件
砥石周速 | 15〜25m/sec(900〜1500m/min) |
---|---|
切り込み量 | 0.02〜0.1mm |
送り速度 | 10〜15m/min |
砥粒タイプ | SD(メタル)、SDC(レジン) |
粒度 | #100〜170(粗工程) #400〜500(仕上げ) |
集中度 | 50〜60 |
研削液 | 水溶性(100:1) |
砥石寸法 | 外径150mm〜204mm |