プラスチックの着色方法
プラスチックの着色方法は大きく2種類あります。プラスチックの原料を溶かして成形する工程で元から着色してしまう方法(内部着色)と、プラスチック製品ができた後から表面だけに塗装やメッキ、蒸着といった方法で色をつける方法(外部着色)です。
ほとんどのプラスチック製品は、成型加工の段階から色をつける方法がとられているため、プラスチックの母材に顔料が練り込まれており、プラスチック製品を仮に切断しても金太郎あめのようにどこを見ても同じ柄(色)になっているのはこれが理由です。
- プラスチックの着色方法|目次
どうやって着色するか
プラスチック製品を作る際は、プラスチックの原料を大元となる原料メーカーから購入しますが、この段階ではプラスチックは種類が違ってもどれも白色や半透明、透明、乳白色といった色合いをしています。多くは、小さなペレットが袋に詰まった状態で購入します。パイプ枕のイメージに近いです。
プラスチックの成形はこの原料を溶かし、金型に高圧で流しこんで冷やして固めることによってなされます。
射出成形機といったプラスチック製品をつくるための成形機に原料ペレット(母材)を投入する際には、マスターバッチと呼ばれる着色専用のペレットも一緒に投入して混ぜる方法がよくとられます。あるいは、母材となる原料のペレットにあらかじめ色を付けた着色ペレットが使われることもあります。この場合は、そのまま使えますが、色違いのものを作る際にはペレット自体を変えないといけない為コスト高になりがちです。色の違うペレットを複数在庫しないといけなくなり、一色きれてしまうと納品できないという事態になります。
マスターバッチは高濃度の顔料が目に見えないほど細かい粉末にして入れてあるペレットで、成形機で母材となるペレットと溶け合って、顔料の小さな「粒」が出てくるとそれがドロドロに溶けたプラスチックの中にほどよく分散されていきます。これによって金型に流し込む前の溶けたプラスチックに着色がなされるという仕組みです。
下図が模式図です。プラスチック原料にあらかじめ添加剤を混ぜてコンパウンドとして混ぜる例もありますが、おおむねこのように、母材となるプラスチック原料、着色剤、添加剤を入れてプラスチック製品は作られます。
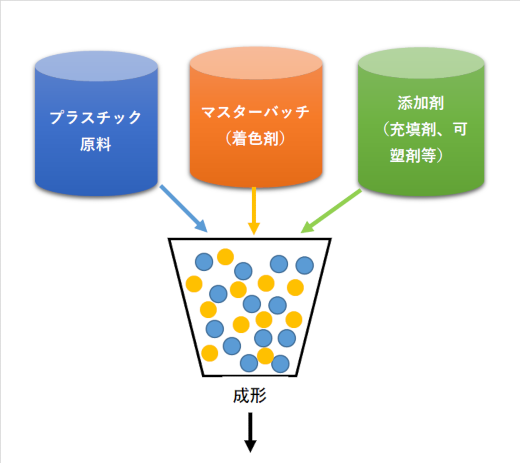
添加剤というのは、可塑剤、難燃剤といったもののほか、充填剤(フィラー)ともいわれるガラス繊維などの強化剤、かさをあげるためのシリカやタルクなどがあります。
着色剤の種類
着色ペレットやマスターバッチ以外にも、ペーストカラーやリキッドカラーと呼ばれる液状の着色剤を入れる方法や、ドライカラーやマスターパウダーと呼ばれる粉末状の着色剤を入れる方法もあります。
プラスチックの原料がペレットで射出成形ならペレット形状のマスターバッチを成形機の材料投入口であるホッパーに入れるだけの方法が使いやすいですが、異なる形状や成形方法の場合は、適宜様々な着色剤を選択することになります。
ドライカラーは粉末なので安いのですが、粉が飛び散ったり、機械に残ったり、計量の手間がかかったり作業が大変です。
液体状になるペーストカラーやリキッドカラー、リキッドマスターバッチは主として母材となるプラスチックが液状の場合に使用されるものです。リキッドマスターバッチは半透明の色付けも可能なため、そうした用途でも使われます。ドライカラーのように飛散のデメリットはありませんが、設備や周囲を汚染してしまうという点ではペレットに軍配が上がります。
着色剤 | 形状 | 使用する主なプラスチック | 特徴 |
---|---|---|---|
マスターバッチ | ペレット | PE、PP、PS、ABS、PVC、PMMA、PA | 成形に使うのと同じプラか相溶性のよい樹脂に顔料を分散させてペレットにしたもの。顔料濃度は20〜80%。現在のプラスチックで主流の着色剤。 |
着色ペレット | ペレット | PS、ABS、PE、PP、PMMA | そのままホッパーに投入して成形できるよう調整されたペレット。顔料濃度は〜10%。成形時の色材の混合や分散の工程が不要となる。着色剤だけでなくフィラーや添加剤を混ぜたコンパウンドの場合は単一のペレット投入で完結。コストの問題からマスターバッチが主流に。 |
ドライカラー | 粉末 | PS、ABS、PE、PP、PMMA、PVC、PC | 顔料を金属せっけんやポリエチレンワックス、アミド系滑剤などに高速撹拌機で混合したもの。他の着色剤に比べ分散性は劣るので繊維やフィルムには適さない。プラスチックと混合が必要で、飛散と汚染がネック。顔料濃度は30〜90% |
マスターパウダー | 粉末 | PVC、PS、PE、PP、ABS | 粉末樹脂の表面に分散処理した染料・顔料を定着させたもの。顔料濃度は5〜30%。ドライカラーより飛散性は低い。顔料濃度が低いので濃色には向かない。 |
樹脂・ワックス分散体 | 粉末 | PVC、PS、PE、PP、ABS | 低融点ワックス系・樹脂成分に顔料を分散、固形にしてから粉砕して粉にしたもの。顔料濃度は30〜80%。ワックス系の材料が母材に入ってしまうので、滑性が上がってしまう。印刷や接着用途には不向き。 |
ペーストカラー | 液状 | PVC、PMMA、PUR、不飽和ポリエステル | 顔料は可塑剤や液状配合物に分散して使用。顔料濃度は20〜80%。長期保管していると沈降分離や再凝集することがあるため、色分かれ防止剤などの添加剤を一緒に使用。 |
リキッドカラー | 液状 | PS、ABS、PE、PP、PVC | 高沸点の液状分散剤に分散して使う。顔料濃度は5〜60%。自動供給システムを備えた成形機に向く。低粘度流体。添加すぎるとスリップを起こす。 |
着色剤は、顔料とプラスチックとの親和性の良い媒体とを混ぜて作りますので、それらの成分はプラスチック本体にも残ることになります。例えば、高級脂肪酸、高級脂肪酸金属塩、低分子量樹脂、ワックス、可塑剤といったものがこの媒体となり、これらの化学物質と顔料を混ぜることで着色剤が出来上がります。
混ぜる際はボールミルやアトマイザー、ビーズミル、アトライター、押し出し機、ニーダー、バンバリーなどが使われます。混ぜられた後、ペレットやリキッド、粉末といった形状に加工され、着色剤が出来上がります。
着色剤に求められる性能
プラスチックの色付けには顔料を使うことが多いですが、大きくは以下の性能が要求されます。またこれらに加え、色を付けるプラスチックの母材との相性も重要で、親和性、溶融速度、拡散性もポイントとなります。
分散性
顔料で色を付ける原理というのは、繊維の染色とは違い、細かい色の粒が均一な状態で材料の中に拡がっていく必要があります。これが分散ですが、上述の通り、射出成型機のなかでも顔料の入ったペレットを溶かしてうまく分散させてやらないと顔料の分散不良を引き起こします。これは市販されているプラスチック製品や容器でもまれにみることがありますが、表面に色の違うブツブツが出てしまったり、薄いフィルムの場合破れてしまうということにもなりかねません。
うまく分散されないとその部分だけ強度不足となったり、外観不良となってしまいます。したがって、分散しやすい顔料であることは非常に重要な要素となります。
耐熱性
射出成形をはじめ、プラスチックを作る際には原料を溶かすために高温をかけます。200℃〜300℃前後にもなるので、この温度に耐えられる顔料や着色剤でないと使うことができません。天然の顔料等で温度に繊細なものもありますがそうしたものは適さないということになります。
また使用している際にプラスチックが溶けるほどの熱でなくても色が変色したり退色してしまっては外観が台無しになりますので、そうした性能も必要とされます。
耐候性
プラスチック製品になったあとは日光に当たることもあると思いますが、プラスチックそのものと同等かそれ以上の耐候性が求められます。もっともプラスチック自体は他の工業材料に比べて紫外線や風雨にさらされることには強くありませんので、公園に放置されたプラスチックのおもちゃ等でひどく色褪せたものが多いのは周知の事実かと思います。
もっとも、プラスチックの劣化前に先に色あせてしまうと、いかにもプラスチック自体がもうボロボロになってしまったように見えるため、こうしたことにならない顔料や着色剤が求められます。
耐酸性や耐アルカリ性
酸性やアルカリ性の物質に触れることは日用品でも工業用品でも多々ありますが、その際に変色してしまう顔料だと困ります。設計用途によってどのようなものに触れるかを想定したうえで、それらに触れても変色しない顔料が求められます。
耐移行性
これは色移りしないかどうかという点です。他の製品や人との接触で色が移ってしまうと使うことができませんので、色移りや溶け出したりしないということが重要です。顔料はもともと「溶けない」色素ですが、プラスチックに「溶ける」色素である染料を使う場合は、色移りには特に気を付ける必要があります。
安全性
用途によっては食品や乳幼児、妊産婦が使用する可能性もあります。使用できる顔料について業界団体が法規制にさらに自主基準を上乗せしたり、表示を明確にしたりといった取り組みがなされていますが、設計段階でもどのような顔料を使用するのか十全な検討が必要な事項といえます。
スポンサーリンク
- 加工材料の性質と特徴(目次)へ戻る
- 「プラスチックの種類と用途、物性について」へ戻る
- プラスチック(樹脂)の種類と記号一覧表
- プラスチックリサイクルマークの数字の意味と種類
- 4大プラスチックとは
- バイオプラスチックの種類と原料|デメリットや課題はどこにあるか
- PFOAの使用と含有製品はいつから規制か|フライパンから繊維、撥水剤、泡消火剤まで
- プラスチックの人体への影響|プラスチックは安全なのか
- プラスチックの比重、密度の一覧表
- プラスチックの融点、耐熱温度の一覧表
- プラスチックの熱変形温度の一覧表
- プラスチックの難燃性|UL規格と酸素指数から見る難燃性の度合い
- プラスチックの引張強さの一覧表
- プラスチックの比熱の一覧表
- プラスチックの熱膨張係数、熱膨張率の一覧
- プラスチックの熱伝導率の一覧
- アロイ化とは
- 熱可塑性樹脂と熱硬化性樹脂の違い
- フェノール樹脂(PF)
- ユリア樹脂(UF)
- メラミン樹脂(MF)
- 不飽和ポリエステル樹脂(UP)
- ポリウレタン(PU)
- ジアリルフタレート樹脂(PDAP)、アリル樹脂
- シリコン樹脂(SI)
- アルキド樹脂
- エポキシ樹脂(EP)
- フラン樹脂
- ナイロン6(PA6):ポリアミド(PA)の一種
- ナイロン66(PA66):ポリアミド(PA)の一種
- ナイロン12(PA12):ポリアミド(PA)の一種
- ポリアミドイミド
- ポリアセタール(POM)
- ポリカーボネート(PC)
- 変性ポリフェニレンエーテル(m-PPE)
- ポリブチレンテレフタラート(PBT)
- GF強化ポリエチレンテレフタラート(GF-PET)
- 超高分子量ポリエチレン(UHPE)
- ポリフェニレンスルフィド(PPS)
- ポリイミド(PI)
- ポリエーテルイミド(PEI)
- ポリアリレート(PAR)
- ポリスルホン(PSF)
- ポリエーテルスルホン(PES)
- ポリエーテルエーテルケトン(PEEK)
- 液晶ポリマー(LCP)
- ポリテトラフルオロエチレン(PTFE)、いわゆるフッ素樹脂
- ポリクロロトリフルオロエチレン(PCTFE)、いわゆるフッ素樹脂
- ポリエチレン(PE)
- ポリプロピレン(PP)
- ポリスチレン(PS)
- アクリロニトリル−スチレン樹脂(AS樹脂)
- アクリロニトリル−ブタジエン−スチレン樹脂(ABS樹脂)
- ポリ塩化ビニル(PVC)
- メタクリル樹脂(PMMA)
- ポリエチレンテレフタラート(PET)
- ポリビニルアルコール(PVA)
- 酢酸セルロース(CA)
- プロピオン酸セルロース(CP)
- 硝酸セルロース(CN)
- ポリ乳酸(PLA)
- フラン-ホルムアルデヒド樹脂(FF)
- エチルセルロース(EC)
- フェノール-ホルムアルデヒド樹脂(フェノール樹脂)(PF)
- ポリスルホン、ポリスルフォン(PSU)
- ポリ塩化ビニリデン(PVDC)
- ポリフッ化ビニリデン(PVDF)
- アイオノマー樹脂
- FRP(繊維強化プラスチック)
- 炭素繊維メーカーの一覧
- プラスチックの黄ばみ除去について
- プラスチックの色によって強度や耐久性に違いはあるか